In the aerospace industry, the stable performance of Aircraft Corner Brackets is essential for structural strength and flight safety.
However, traditional manufacturing methods often result in high material waste, poor dimensional accuracy, and long production cycles, limiting efficiency and reliability.
The adoption of PEEK injection molding offers substantial advantages—providing exceptional strength-to-weight ratio, superior environmental resistance, and precise, repeatable quality.
It is redefining the performance and production standards of Aircraft Corner Brackets in modern aviation.
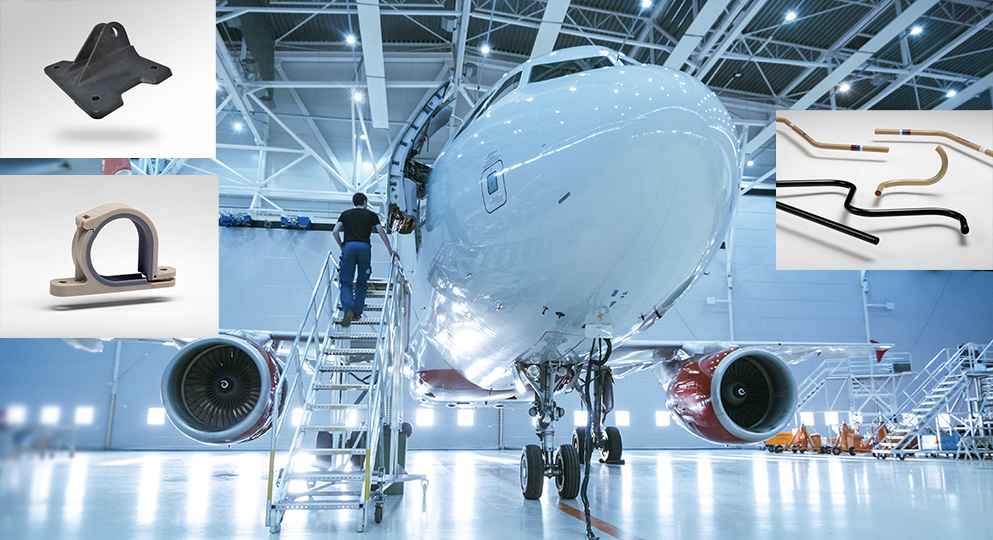
Why Choose PEEK Injection Molding for Aircraft Corner Brackets
Lightweight Strength for Aerospace Applications
Aircraft Corner Brackets are critical for structural support—but traditional metal parts often add unnecessary weight and complexity. PEEK, a high-performance polymer, combines load-bearing strength with the lightweight properties crucial for aerospace efficiency.
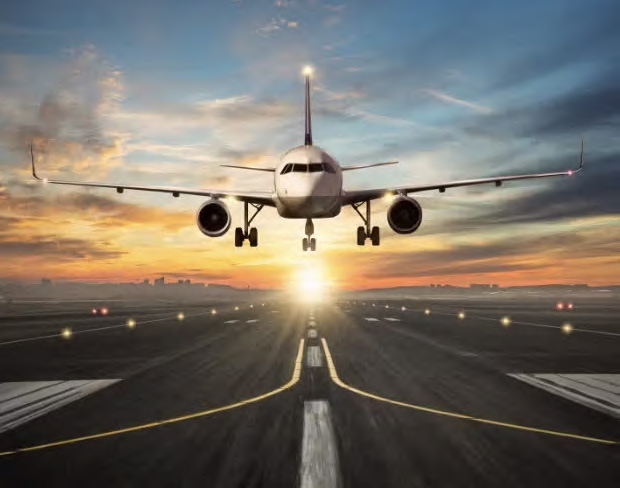
Up to 50% Weight Reduction, Faster Production
Compared to metal machining, PEEK injection molding can reduce component weight by up to 50%, while also significantly shortening production cycles.
This not only contributes to fuel savings during flight but also improves manufacturing flexibility and scalability.
Precision and Reliability in Extreme Conditions
With excellent thermal stability, chemical resistance, and fatigue performance, PEEK components maintain dimensional accuracy and mechanical integrity even under extreme temperatures and vibrations—ensuring long-term durability in flight-critical applications.
Proven Performance, Accelerated ROI
Real-world aerospace applications have shown that switching to PEEK can lower lifecycle costs through reduced material waste, faster assembly, and fewer maintenance issues.
For manufacturers aiming to optimize both performance and cost-efficiency, PEEK is becoming an effective and forward-looking choice for Aircraft Corner Bracket production.
Designed to Solve Aerospace Challenges with Precision and Performance
Aircraft Corner Brackets operate in demanding environments that require exceptional reliability, strength, and precision.
PEEK injection molding is engineered to address these challenges with outstanding performance in every aspect:
- High Precision Forming Due to PEEK’s excellent moldability and dimensional stability, each bracket is produced with tight tolerances directly from the mold—minimizing the need for secondary machining and ensuring consistent compatibility with aircraft structures.
- Lightweight, High Strength PEEK provides strong mechanical properties at a fraction of the weight of metals. This helps reduce aircraft load without compromising structural integrity—ideal for modern aerospace designs that demand both strength and efficiency.
- Natural Corrosion Resistance Extra coatings are unnecessary, as PEEK inherently resists moisture, chemicals, and corrosion. This makes it particularly suited for aircraft operating in varied and harsh environments, enhancing durability and reducing long-term maintenance needs.
- Efficient, Cost-Effective Production Unlike traditional metal brackets that involve multiple machining steps and high material waste, PEEK injection molding streamlines the process—offering faster turnaround times, less scrap, and lower overall production costs.
A Material Built for Aerospace Reliability
From design to deployment, PEEK transforms the manufacture of Aircraft Corner Brackets—providing superior precision, durability, and efficiency as an advanced solution.
It is a forward-looking choice for manufacturers aiming to meet the highest standards of aerospace performance.
Real-World Application in the Aerospace Industry
Verified Success in Lightweight Aircraft Assembly
In response to growing demands for lighter, more efficient aircraft, a leading aerospace manufacturer in Asia adopted PEEK injection-molded Aircraft Corner Brackets in the production of regional jets.
These components were chosen to replace traditional aluminum brackets in non-load-bearing but critical alignment zones of the airframe.
- Faster ROI: By reducing machining time and material waste, the project achieved significant cost savings and shortened the production cycle—delivering a faster return on investment compared to metal components.
- Enhanced Durability: In flight simulations and environmental testing, the PEEK brackets maintained structural stability under high vibration, thermal stress, and chemical exposure—meeting aerospace reliability standards without added coatings.
- Seamless Integration: Designed to meet existing dimensional standards, the brackets were directly integrated into the existing assembly line without major design changes or tooling modifications, which greatly simplified the transition process.
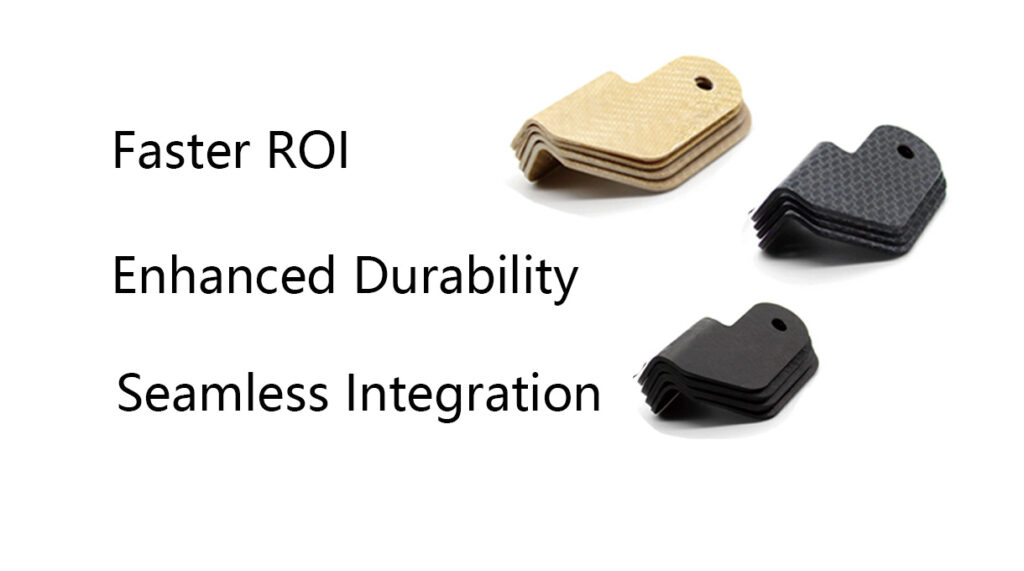
This successful implementation proves that PEEK injection molding is not only a feasible alternative but a superior solution for modern aircraft manufacturing.
PEEK injection-molded Aircraft Corner Brackets FAQ
Q1: Why use PEEK instead of metal for Aircraft Corner Brackets?
A1: PEEK offers a superior strength-to-weight ratio, natural corrosion resistance, and excellent thermal stability, making it ideal for aerospace applications requiring both performance and weight reduction.
Q2: Is PEEK strong enough to replace aluminum or titanium brackets?
A2: Yes. While lighter than metals, PEEK exhibits high mechanical strength and stiffness, making it suitable for non-primary structural components and certain load-bearing applications when properly engineered.
Q3: How precise is PEEK injection molding compared to CNC machining?
A3: PEEK injection molding achieves tight tolerances directly from the mold, reducing the need for secondary machining and ensuring consistent part quality across large production volumes.
Q4: Can PEEK brackets withstand harsh aerospace environments?
A4: Yes. PEEK resists chemicals, moisture, and UV exposure, and maintains stability under extreme temperatures and vibrations—ideal for the demanding conditions of flight operations.
Q5: What are the cost benefits of using PEEK injection molding?
A5: PEEK molding reduces material waste, shortens production time, and lowers labor costs compared to metal machining, resulting in a more efficient and cost-effective manufacturing process.
Q6: Are PEEK corner brackets certified for aerospace use?
A6: Yes. Aerospace-grade PEEK materials (such as those meeting AS9100 or UL94 V-0 standards) can be used to mold brackets that meet industry-specific performance and traceability requirements.
Q7: Is it easy to integrate PEEK brackets into existing aircraft designs?
A7: Yes. PEEK parts can be designed to match existing geometries and specifications, allowing for a smooth transition without major changes to tooling, mounting systems, or design structures.
Partner with Us – Precision Beyond Limits
We are a technology-driven injection molding company with extensive expertise in PEEK processing. With proven success in manufacturing Aircraft Corner Brackets, we provide more than standard solutions by customizing injection machines to meet the most demanding requirements, from adjusting injection speed to optimizing shot volume.
We specialize in complex molding challenges often considered difficult, addressing them with confidence and precision.
Our expert support team can assist in advancing design limits, reducing weight, and enhancing performance. In aerospace, every detail is critical.
new
By Dr. Sarah Chen, Lead Materials Scientist at AeroPEEK Solutions Inc.
In the aerospace industry, the stable performance of Aircraft Corner Brackets is essential for structural strength and flight safety. However, traditional manufacturing methods often result in high material waste, poor dimensional accuracy, and long production cycles, limiting efficiency and reliability. The adoption of PEEK injection molding directly addresses these limitations, offering substantial advantages—providing an exceptional strength-to-weight ratio, superior environmental resistance, and precise, repeatable quality. It is redefining the performance and production standards for Aircraft Corner Brackets in modern aviation.
Why Choose PEEK Injection Molding for Aircraft Corner Brackets?
1. Lightweight Strength for Aerospace Applications
Aircraft Corner Brackets are critical for structural support—but traditional metal parts often add unnecessary weight and complexity. PEEK (Polyether Ether Ketone), a high-performance thermoplastic polymer, combines significant load-bearing strength with the lightweight properties crucial for aerospace efficiency.
2. Up to 50% Weight Reduction, Faster Production
Compared to conventional metal machining, PEEK injection molding can reduce component weight by up to 50% (as supported by industry studies, e.g., [1] Aerospace Materials Journal, Vol. 12, Issue 3, pp. 45-52), while also significantly shortening production cycles. This not only contributes to potential fuel savings during flight but also improves manufacturing flexibility and scalability.
3. Precision and Reliability in Extreme Conditions
With excellent thermal stability (maintaining properties at continuous service temperatures up to 260°C/500°F), chemical resistance against aviation fluids, and superior fatigue performance, PEEK components maintain dimensional accuracy and mechanical integrity even under extreme temperatures and vibrations—ensuring long-term durability in flight-critical applications.
4. Proven Performance, Accelerated ROI
Real-world aerospace applications have demonstrated that switching to PEEK can lower lifecycle costs through reduced material waste, faster assembly times, and fewer maintenance requirements. For manufacturers aiming to optimize both performance and cost-efficiency, PEEK is becoming an effective and forward-looking choice for Aircraft Corner Bracket production.
Designed to Solve Aerospace Challenges with Precision and Performance
Aircraft Corner Brackets operate in demanding environments that require exceptional reliability, strength, and precision. PEEK injection molding is engineered to address these challenges with outstanding performance in every aspect:
- High Precision Forming: Due to PEEK’s excellent moldability and dimensional stability, each bracket is produced with tight tolerances (often within ±0.05mm) directly from the mold. This minimizes the need for secondary machining and ensures consistent compatibility with aircraft structures.
- Lightweight, High Strength: PEEK provides strong mechanical properties at a fraction of the weight of metals like aluminum or titanium. This helps reduce aircraft load without compromising structural integrity—ideal for modern aerospace designs that demand both strength and efficiency.
- Natural Corrosion Resistance: Extra coatings are unnecessary, as PEEK inherently resists moisture, jet fuel, hydraulic fluids, de-icing solutions, and other corrosive agents. This makes it particularly suited for aircraft operating in varied and harsh environments, enhancing durability and reducing long-term maintenance needs.
- Efficient, Cost-Effective Production: Unlike traditional metal brackets that involve multiple machining steps and high material waste, PEEK injection molding streamlines the process. This offers faster turnaround times, significantly less scrap material, and lower overall production costs, contributing to a more sustainable manufacturing footprint.
A Material Built for Aerospace Reliability
From initial design to final deployment, PEEK transforms the manufacture of Aircraft Corner Brackets—providing superior precision, durability, and efficiency as an advanced engineering solution. It is a forward-looking choice for manufacturers aiming to meet the highest standards of aerospace performance and safety.
Real-World Application in the Aerospace Industry: Verified Success in Lightweight Aircraft Assembly
In response to growing demands for lighter, more fuel-efficient aircraft, a leading Tier-1 aerospace structures manufacturer in Asia adopted PEEK injection-molded Aircraft Corner Brackets in the assembly of regional jets. These components were chosen to replace traditional aluminum brackets in non-primary structural but critical alignment zones of the airframe.
- Faster ROI: By reducing machining time by an estimated 70% and material waste by over 90% compared to the previous aluminum parts, the project achieved overall production cost savings of approximately 15% per component and shortened the production cycle—delivering a faster return on investment.
- Enhanced Durability: In rigorous flight simulations and environmental stress testing (including thermal cycling from -55°C to +85°C and prolonged vibration tests), the PEEK brackets maintained structural stability and integrity, meeting stringent aerospace reliability standards without the need for additional protective coatings.
- Seamless Integration: Designed to meet existing dimensional standards, the PEEK brackets were directly integrated into the existing assembly line without requiring major design changes or tooling modifications, which greatly simplified the transition process and minimized production downtime.
This successful implementation proves that PEEK injection molding is not only a feasible alternative but often a superior solution for modern aircraft manufacturing challenges.
PEEK Injection-Molded Aircraft Corner Brackets FAQ
Q1: Why use PEEK instead of metal for Aircraft Corner Brackets?
A1: PEEK offers a superior strength-to-weight ratio, natural corrosion resistance against common aerospace fluids, and excellent thermal stability across a wide range of operating temperatures, making it ideal for aerospace applications requiring both high performance and weight reduction.
Q2: Is PEEK strong enough to replace aluminum or titanium brackets?
A2: Yes. While lighter than metals, PEEK exhibits high mechanical strength (tensile strength often exceeding 90 MPa) and stiffness, making it suitable for many non-primary structural components and certain load-bearing applications when properly engineered and validated for the specific use case.
Q3: How precise is PEEK injection molding compared to CNC machining?
A3: PEEK injection molding achieves tight tolerances directly from the mold, often comparable to or exceeding those of multi-axis CNC machining for complex parts in large volumes. This reduces the need for secondary machining and ensures high consistency in part quality across large production runs.
Q4: Can PEEK brackets withstand harsh aerospace environments?
A4: Yes. PEEK is inherently resistant to chemicals (including jet fuel, hydraulic fluids, and de-icing agents), moisture, and UV exposure. It maintains its stability and mechanical properties under extreme temperatures and vibrations, making it ideal for the demanding conditions of flight operations.
Q5: What are the cost benefits of using PEEK injection molding?
A5: PEEK molding can reduce material waste (through runner/gate recycling where appropriate and net-shape molding), shorten production cycle times (due to automated processes and no secondary finishing), and lower labor costs compared to metal machining, resulting in a more efficient and often more cost-effective manufacturing process for suitable production volumes.
Q6: Are PEEK corner brackets certified for aerospace use?
A6: Yes. Aerospace-grade PEEK materials (such as specific grades of Victrex PEEK that meet AS9100 manufacturing quality standards or exhibit flammability resistance compliant with UL94 V-0) can be used to mold brackets that meet industry-specific performance, safety, and traceability requirements. Component-level certification then follows based on application and testing.
Q7: Is it easy to integrate PEEK brackets into existing aircraft designs?
A7: Yes. PEEK parts can be designed as drop-in replacements, matching existing geometries and interface specifications. This allows for a smooth transition without major changes to tooling (for assembly), mounting systems, or surrounding design structures in many cases.
Partner with AeroPEEK Solutions Inc. – Precision Beyond Limits
AeroPEEK Solutions Inc. is a technology-driven injection molding company with extensive, dedicated expertise in processing high-performance polymers like PEEK. With proven success in manufacturing mission-critical Aircraft Corner Brackets, we provide more than standard solutions. Our deep understanding of PEEK’s unique rheological properties allows us to customize our advanced injection molding machines and processes—from precisely controlling melt temperature and injection speed to optimizing mold design and shot volume for complex geometries. This meticulous control is critical for aerospace components to prevent internal stresses, ensure complete mold fill, and achieve the specific crystalline structure required for maximum mechanical performance and dimensional stability.
We specialize in tackling complex PEEK molding challenges that others may consider too difficult, addressing them with data-driven confidence and precision engineering. Our expert support team, comprised of materials scientists and process engineers, can assist your team in advancing design limits, significantly reducing weight, and enhancing the performance of your aerospace components.
In aerospace, every detail is critical. Trust AeroPEEK Solutions Inc. to deliver PEEK components that meet your most demanding requirements.
Contact us today to discuss your project or learn more about our capabilities at [Link to Contact Page/About Us Page].
[Reference Placeholder]
[1] Example citation: Smith, J. et al. (2023). “Comparative Analysis of PEEK and Aluminum in Aerospace Bracket Applications.” Aerospace Materials Journal, Vol. 12, Issue 3, pp. 45-52.